Plastic bag printing machine for sale
Type:Flexographic Printer | Condition:New | Plate Type:Letterpress | Place of Origin:Guangdong China (Mainland) |
Brand Name:Disen | Model Number:DS-YT-2600-13 | Usage:Paper Printer,Card Printer,Bill Printer,Cloths Printer,plastic printer | Automatic Grade:Automatic |
Color & Page:Two Colors | Voltage:380V | Gross Power:8kW | Dimensions(L*W*H):2300*1600*2200mm |
Weight:1800kg | Certification:CE | Name:Plastic bag printing machine for sale | Max. Web Width:600mm |
Max. Effective Printing Width:560mm | Range of Repeat Printing Length:191~914mm | Max. Diameter of Roll Material:Diameter 450mm | Printing Speed:5~50m/min |
Printing materials:Web, non-woven fabrics,woven cloth,PVC,OPP,BOPP,PE,etc | Overprint precision:+-0.3(mm) | Warranty:one year | Plate Thickness:2.38mm |
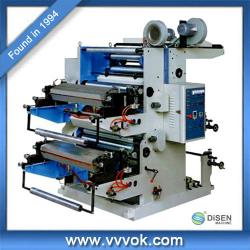
Product Description |
Double-color Flexography Printing Machine Introduction: Application: Introduce sensitization resin as flexible printing plate, suitable for printing such packing materials as polyethylene, polypropylene bag, cellophane and roll paper, etc. It is a kind of ideal printing equipment for producing paper packing bag for food, supermarket handbag, vest bag and clothes bag, etc. Flexography printing machine Performance and Features: 1. Easy operation, flexible starting, accurate color register. 2. The meter counter can set printing quantity according to the requirements. Stop the machine automatically at the quantity or when the material is cut off. 3. Pneumatic printing cylinder lift and lower, it will stir the printing ink automatically after lifting. 4. The printing ink is spread by the anilox cylinder with even ink color. 5. Reliable drying system coordinated with high-speed rotation, it will automatically break circuit when the machine stops. 6.360°continuous and adjustable longitudinal register device. 7. The frequency control of motor speed adapts to different printing speeds. 8. There are Jogging/Stopping buttons on the plate roller base and material rolling rack so as to make it easy operate the machine when the plate is installed. Flexography printing machine Main Technical Variables:
|
Product Images |
Plastic bag printing machine for sale Plastic bag printing machine for sale Plastic bag printing machine for sale Plastic bag printing machine for sale
|
Product Related Information |
Flexography (often abbreviated to flexo) is a form of printing process which utilizes a flexible relief plate. It isessentially a modern version of letterpress which can be used for printing on almost any type of substrate, including plastic, metallic films, cellophane, and paper. It is widely used for printing on the non-porous substrates required for various types of food packaging (it is also well suited for printing large areas of solid color). Process overview 1. Platemaking The second method used a computer-guided laser to etch the image onto the printing plate. Such a direct laser engraving process is called digital platemaking. Companies such as AV Flexologic, Polymount and Screen from The Netherlands are market leaders in manufacturing this type of equipment. The third method is to go through a molding process. The first step is to create a metal plate out of the negative of our initial image through an exposition process (followed by an acid bath). This metal plate in relief is then used in the second step to create the mold that could be in bakelite board or even glass or plastic, through a first molding process.Once cooled, this master mold will press the rubber or plastic compound (under both controlled temperature and pressure) through a second molding process to create the printing plate. 2. Mounting For every colour to be printed, a plate is made and eventually put on a cylinder which is placed in the printing press. To ensure an accurate picture is made, mounting marks are made on the flexographic plates. These mounting marks can be microdots (down to 0.3 mm) and/or mounting crosses. To make a complete picture, regardless of printing on flexible film or corrugated paper, the image transferred from each plate has to fit exactly in the images transferred from the other colors.Highly accurate and specific machinery is made for mounting these plates on the printing cylinders. One of the latest advances in this field is Fully Automatic Mounting Machine (FAMM), for which AV Flexologic won the FTA Technical Innovation Award in 2007. 3. Printing A flexographic print is made by creating a positive mirrored master of the required image as a 3D relief in a rubber or polymer material. Flexographic plates can be created with analog and digital platemaking processes. The image areas are raised above the non image areas on the rubber or polymer plate. The ink is transferred from the ink roll which is partially immersed in the ink tank. Then it transfers to the anilox roll (or meter roll) whose texture holds a specific amount of ink since it is covered with thousands of small wells or cups that enable it to meter ink to the printing plate in a uniform thickness evenly and quickly (the number of cells per linear inch can vary according to the type of print job and the quality required).To avoid getting a final product with a smudgy or lumpy look, it must be ensured that the amount of ink on the printing plate is not excessive. This is achieved by using a metal scraper, called a doctor blade. The doctor blade removes excess ink from the anilox roller before inking the printing plate. The substrate is finally sandwiched between the plate and the impression cylinder to transfer the image.The sheet is then fed through a dryer, which allows the inks to dry before moving on.In the case a UV ink is used, the sheet does not have to be dried, but is dried from UV rays.
Operational overview 1. Fountain roller 2. Anilox roller 3. Plate cylinder 4. impression cylinder Flexographic printing inks There are five types of inks that can be used in flexography: solvent-based inks, water-based inks, electron beam (EB) curing inks, ultraviolet (UV) curing inks and two-part chemically-curing inks (usually based on polyurethane isocyanate reactions), although these are uncommon at the moment.Water based flexo inks with particle sizes below 5 µm may cause problems when deinking recycled paper. Ink controls Applications |
DiSen Company Show |
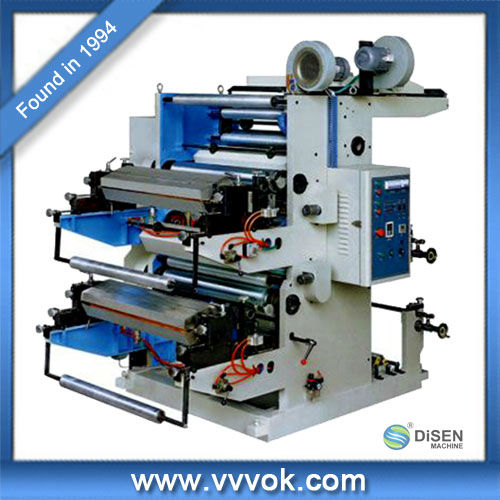
Packaging Detail:wooden case,Overall Dimension:2300*1860*2145mm,weight:1800kg |
Delivery Detail:Ten days |