Particle board machinery / chipboard plant
Condition:New | Type:Particle board production line | Place of Origin:Shandong China (Mainland) | Brand Name:XIANGYING |
Model Number:PBL-4*8/1200 | Voltage:380V/415V | Warranty:One year | After-sales Service Provided:Engineers available to service machinery overseas |
Working type:PLC, Full automatic | Total pressure:1200T | Layer:6-30 | Board size:4*8'(1220*2440mm) |
Board thickness:8-25mm | Yearly capacity:15000CBM-150000CBM | Raw material:Bagasse, Wood branch, Log, Waste wood, Saw dust, Leftovers | Glue type:Urea-formaldehyde glue |
Worker:about 15 persons for each shift | Working time:22.5h/day, 3 shifts; 300days/yr |
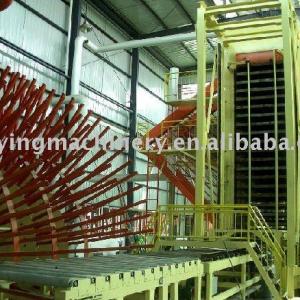
Particle board production line, Chip board production line, woodworking machine, Chip board plant
Particle board is made from small-diameter wood, branches, wood residues and non-wood agricultural residues via Chip preparation, drying, spreading and hot press section. Finished boards can be used for furniture, building, packing, vehicle and decoration and lamination.
1. Chip preparation section
Raw material is reduced into qualified chips by the drum chipper, then the chips are transported to the chip bin, and then feed to the knife-ring flaker by which the chips are turned to flakes, then the flake stored in wet flake bin.
2. Drying and sifting section
The flakes discharged from the wet flake bin are conveyed to the rotary dryer. Qualified core flakes are stored in core flake bin; oversize flakes are send to mill to be re-crushing, and transported to surface flake bin.
3. Glue regulating and applying section
After scaled, the core and surface flakes are to be effectively and uniformly mixed with qualified glue independently in their glue mixers respectively.
4. Forming and hot-pressing section
The surface and core flakes are sent into classi-forming machine, and forming on the mat conveyor uniformly. After processes of metal remover, pre-press, lengthwise saw, cross saw, accelerate conveyor, scaling conveyor, storing conveyor and loading conveyor, mats are transported to carrier and then to hot press. Rough boards after pressing are pushed to unloader via pallet.
5. Cooling and sizing section
The rough board is conveyed to star-cooler for cooling, then the rough board goes through side trimming saw and become a qualified particle-board, stacked on the hydraulic lift.
6. Sanding Section
The board are sanded, checked and stored .
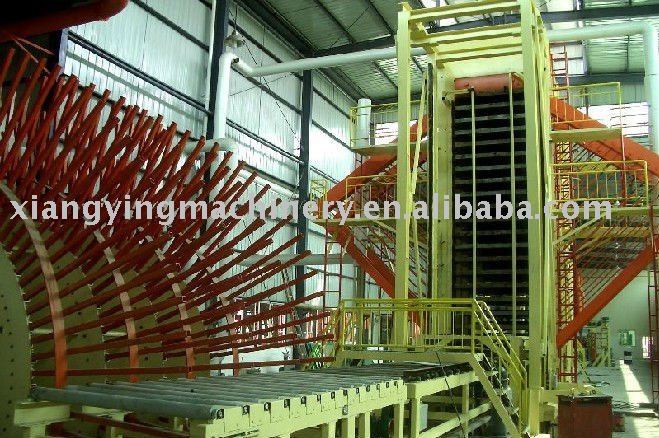
Packaging Detail:export safety package. |
Delivery Detail:90 days |