Mobile Asphalt Plant
Capacity : Approximately up to 80 TONS / HR, Wide Range of Mix Recipes with six ingredients - details see: https://www.machineto.com/mobile-asphalt-plant-10115368
Place of Origin:Pakistan | Brand Name:Mobile Auto Asphalt Plant | Capasity up to 80 ton/hr:heigh efficiency drying |
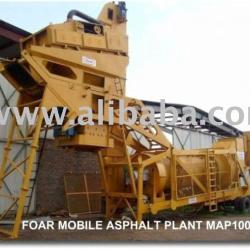
FOAR Mobile Asphalt Mix M – 80 is compact, reliable & flexible piece of new technology with following outstanding features.
- Capacity : Approximately up to 80 TONS / HR (Please refer to note page 2)
- Wide Range of Mix Recipes with six ingredients
- Meets Environmental Standards (After inclusion of 2nd stage of air cleaning equipment)
- High efficiency drying, aggregate grading, homogenous mixing, best control.
- Drying weighing & mixing section travels as a single mobile unit.
- Cold aggregate feed section travels as a single mobile unit.
- Compact transportable or semi-trailer mobile ancillaries like thermal oil heater & dust collector, piping pumps, etc.
Crane free rapid erection of drying / mixing section. • Hydraulics pack and jacks included for crane-free rapid erection of drying/mixing section. Quick Relocation & Installation
Hopper capacity 9.5 m3 each Feeder belt 50 mm wide & 1500 mm centre dust and equipped with 2.2 kW drive placed below hopper having capacity of 100 – 120 Tons / Hr per feed. Feeder discharge in line with allocating conveyor Collecting conveyor 500 mm wide continuous belting, driven through variable speed AC geared motor. Integral collecting conveyor with S bend extension to deliver material directly into drier drum
FOAR rapid inclined vibrating screen 1.5m x 3.0 m, double deck arranged to separate 4 sizes plus rejects.Eccentric shaft with additional weights to adjust screen amplitude, and running in two grease lube spherical roller bearings.Screens mounted on steel coil compression springs. Manual winch arrangement to reposition screen for travelling.
TWIN SHAFT PADDLE MIXER Twin shaft paddle mixer design providing homogeneous mixing in minimum time cycle.Nominal ‘wet’ mixing time of 35 to 40 seconds. Side liners and paddle tips are made of wear-resisting alloy casting. Reversible and adjustable paddle tips for maximum wear life.
HOPPERS Aggregate weigh hopper, mounted on 4 load cells, with remotely operated radial discharge door.Filter weigh hoppers mounted on 3 load cells, with butterfly discharge valve. Bitumen weigh hoppers mounted on 3 loads cells with automatically operated butterfly discharge valve. Accumulated accuracy: Aggregate <+ 0.5%, Bitumen & Filler <+ 0.3%.
FOAR rapid inclined vibrating screen 1.5m x 3.0 m, double deck arranged to separate 4 sizes plus rejects. Eccentric shaft with additional weights to adjust screen amplitude, and running in two grease lube spherical roller bearings. Screens mounted on steel coil compression springs. Manual winch arrangement to reposition screen for travelling. Equipped with over size aggregate chute discharging in fron
Hot stone elevator arranged with compact shaft-mounted motor/gearbox unit (with automatic backstop).
Quality fabrication, divided into 4 compartments. Each compartment fitted with overflow chute and radial discharge door, delivering aggregate to aggregate hopper.
Dryer, 1500 mm x 6000 mm long, equipped with fully automatic control oil burner and specially designed lifter pattern optimized for maximum heat transfer efficiency, provides continuous aggregates input to the mixing plant.
GI cladding & rock wool thermal insulation can be provided as an option, all around drier ensuring minimum heat loss and higher thermal efficiency, with low noise operation.
Four support rollers, two thrust rollers, chain drive to cylinder from 25 HP AC geared motor & controls to rotate the drier at a certain speed, a temperature probe in discharge chute to monitor the flue gases temperatures.
Consisting of axial flow multi cyclone capable of handling 22000 m3/Hr with screw conveyor transferring dust to hot elevator for adding back to system.
Secondary Dust Collection system capable of handling 30,000 m3/Hr dusty air is provided as optional equipment. Nomex or equivalent filter bags are used for high temperature filtration ensuring air cleaning to 99.5% purity. Fully automatic state of art “pulse air jet type” filter bag cleaning system is provided with computerized control, screw conveyors to transfer dust back to mix or to storage silo.
FOAR also suppliers dust conditioner to make pollution free disposal of dust from storage Silo to transport vehicles
- All components used are of top quality, with ISI Certification wherever available.
- All moving parts and electrical parts are provided with safety covers.
- Ease of lubrication and dismantling has been built into the design for efficient maintenance and repair.
- Fabricated parts are thoroughly cleaned and treated before painting.
- Manufacturing is done with advanced, internationally recognised, techniques.
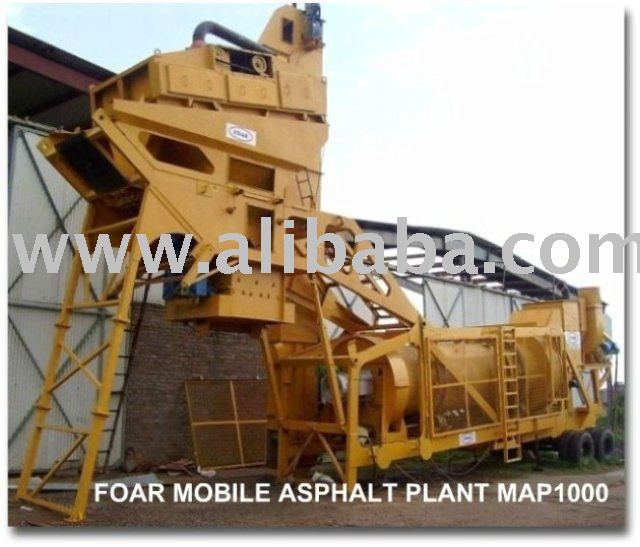
Packaging Detail:Mobile |
Delivery Detail:Ex stock |