MDF production line
Condition:New | Type:MDF production line | Place of Origin:Shandong China (Mainland) | Brand Name:xiangying |
Model Number:MDF | Voltage:380V | Power(W):KW | Warranty:1year |
After-sales Service Provided:Engineers available to service machinery overseas |
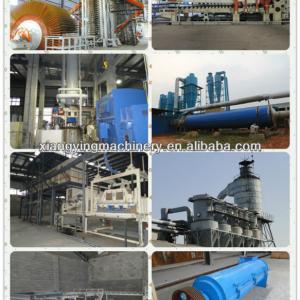
MDF production line
MDF production line with different capacity. baord size 1220x2440mm.
Capacity/Y: 30000CBM, 50000CBM, 80000CBM, 100000CBM, etc.
MDF is a kind of WBP with density of 450-880kg/cm3 which is made from wood, branches and wood residues.
1.Chip preparation
Wood, branches and wood residues are cut into chips of definite size. Chips from chips silo will be screened or airgraded to remove fines, soil and stones.
2. Fiber preparation section
Chips are transported to upper bin of refiner, and positively fed to digester by screw feeder for steaming. Steamed chips will be disintegrated to fiber under the force of heat and mechanism. Mix drying medium and wet fiber which is in the state of suspension with the help of high pressure air flow, and thus exhaust moisture in fiber via drying medium to get dry fiber. Dry fiber falls on belt conveyor through cyclone discharge valve, and then be transported to dry fiber bin for storage.
3. Glue mixing and applying section
Process of glue applying before drying is adopted. Feed molten paraffin and water-proof additive to refiner. Paraffin is mixed with fiber uniformly under the force of refiner plates. Glue is transported to the blow line of fiber discharge valve. This section can be controlled by PLC or computer.
4.Fiber drying section
The fibers after mixing with glue is transported to drying ducts along with steam, and transported to cylcone separator by hot air. And thus the water in the fibers is drained out with hot air.
5. Mat-forming and hot-pressing section
The fiber after drying is transported to the above of forming machine, and uniformly spread on the conveying mesh belt in the way of air-flow. Vacuum box equipped below the mesh belt provides negative pressure and air will be removed via mesh belt, fiber stays on mesh belt and thereafter forms mats gradually. Fluffy mats will be pressed by pre-press. Pressed mats are cut into definite length by longitudinal and transversal saw, then transported to loader passing through accelerating conveyor, storage conveyor and extension conveyor. When finishing loading mats, carriage in the loader will feed conveying belt and mats into hot press, at the same time, shovel head at the front end of conveying belt pushes out pressed board. When carriage comes to terminal, boards have been into unloader, and mats also arrives to due position. Carriage returns, conveying belt turns forward. Mats are in the relative still state and stay on the platen of press when velocity of conveying belt is the same as the returning speed of carriage. Glue in the mats cures, thanks to temperature and pressure in hot press, and hence boards with definite intensity and thickness form. Rough boards will be put on support via unloader. Outfeeding conveyor will unload boards one after another to next section when cage comes down.
6. Cooling, sizing and sanding section
Rough boards after air cooling are turned into cut-to-size boards via longitudinal and transversal saw. And then cut-to-size boards are sanded, sorted, stacked and packed for storage
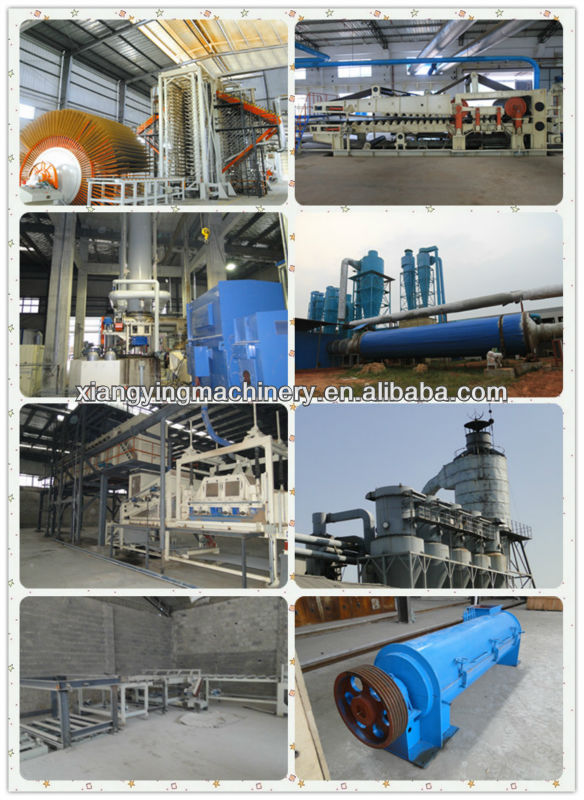
Packaging Detail:Export safe packing |
Delivery Detail:90 days |