Internationally renowned brands ,LB1000 ASPHALT MIXING PLANT long warranty
Place of Origin:Guangdong China (Mainland) | Brand Name:RP | Model Number:LB1000 |
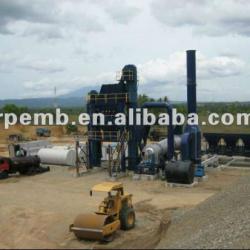
2. Construction Characteristic
1) Hopper adjusts quantity of material by leather belt in control room.
2) Optimization designed Turndown rig of dryer which has a logical placement is either to improve efficiency or to avoid overheat of aggregate.
3) Hot material elevator use loop chain transmission, life is long, convenient maintenance, fine reliability.
4) Screening plant which uses middle four layers circular screen of single axle is high in efficiency, not easily blocked. Vibrancy bearing which has a cooler fan solves middle vibrancy bearing overheat problem. Screening plant reduces influence of noise on complete appliance by second shock absorption. Consequently decreasing influence on measuring system. The body of screen is airproofed in the cover to avoid pollution of dust, the cover is locked by spring device, easily disassembled.
5) Door of Storage bin is single one which is big gap, avoiding block and leakage of material.
6) Door of measuring bin is in compaction and reliable, also avoiding block and leakage of material, shaft sleeve of bin is made of graphite, dry lubrication, no needing lubricant at work.
7) Bitumen is nebulized and injected into the mixer coercively, mixed equality, time is reduced accordingly.
8) Shaft tip of mixer uses chevron seal, avoiding leakage of material.
9) Lining board in the mixer is high intension bearing material, after abration of blade, it’s direction can be changed, then using it newly.
10) Discharge door of mixer is form of push and pull, discharge hole is big, time of discharge is short. Dependability is good.
11) Dust collection system is a two grades system, the first is cyclone collection, after collection the filler goes into the hot material elevator and recycled. The second grade is wet collection, which is made up of two water pumps drenching the material. Efficiency of dust collection is improved very strongly. Bag collection is used in the second collection.
12) Complete appliance is controlled by industrial computer, easy to study and understand, precision is high, Dependability is good. Printer can print working form. Electrical components use oversea and domestic famous brand products. Dependability of hardware is guaranteed.
3. Working process
Asphalt mix material is made up of bitumen, aggregate, powder. The main work of Asphalt mixing plant is to mix the hot aggregate with bitumen, powder after they are measured by electronic scale, producing asphalt mix material which has certain graduation , certain temperature.
Working process as follows:
1) Loaders load various sandstone material into the cold aggregate hoppers, material is conveyed to the dry device after quantity of various material in each hopper is roughly adjusted. Material is conveyed to vibrating screen upstairs by elevator. By screened, various hot aggregates are screened into hot hopper apart according to graduation, by controlling small gate under hot hopper, material is put into measuring hopper, then the quantity can be confirmed. Measuring which is a control system is made up of electronic sensor, electronic scale, small gate, pneumatic cylinder, solenoid valve, controlling quantity of each material in hoppers by opening and closing gate. After measured, material is put into mix cylinder.
2) Hot bitumen is conveyed into mixing plant and injected into mix cylinder after measured by bitumen measuring jar.
3) Filler is elevated to filler storehouse of mixing plant and put into mix cylinder after measured.
Three materials are mixed and changed into final product.
Model and productive capacity
Model | LB1000 |
Batch of mixer | 1000Kg |
Capacity of hopper(4pieces) | Width of each hopper | Height of each hopper | Adjustable-speed motor(4pieces ) | Electromotor of Motorized head pulley(1pieces) | Belt width |
7 m³ | 3000mm | 3620mm | 1.5Kw | 2.2Kw | 500mm |
Electromotor of Motorized head pulley(1 piece) | 3Kw |
Belt width | 500mm |
3. drying and fuel supply system
1) Dryer
Type | acclivitous cylinder and friction wheel drive |
Capacity | 100t/h |
Spec | 1800mmx8332mm |
Reducer(4pieces) | 7.5Kw |
2) Burner
Diesel burner
3) Burner
Type | High-pressure nebulized |
Capacity | 550kg/h |
4) Fuel pump
Type | gear pump |
Capacity | 600L/h |
Pressure | 10Kg/cm² |
Electromotor | 1.1Kw |
Fuel tank | 10m³ |
5) Blower Fan
Type | centrifugate |
Capacity | 120m³/min |
Electromotor(1piece) | 22Kw |
Fuel consumption | 6.5-7 liters/ton asphalt(normal working situation and eligible aggregate) |
4. Filler elevator
Electromotor(1piece) | 2.2Kw |
5. Hot elevator
Electromotor(1piece) | 7.5Kw |
6. Screen system
Middle vibrator which has four specs and four floors, bearing cool with fan, two grade damping, airproof between screen and hot bin.
Spec of screen mesh 3x4 7x7 16x16 24x24mm
We can also supply special mesh size according to customer demand.
Electromotor(1piece) | 5.5Kw |
Capacity | 85t/h |
7.Mixer
Type | horizontal and double axle, pull and push material gate |
Electromotor of Reductor(1piece) | 30Kw |
8.Framework
9. Aggregate measuring device
Sensor(3pieces) | 1000kgs |
10.Filler measuring device
Sensor(3pieces) | 200kgs |
Filler feed electromotor(1piece) | 0.75Kw |
11.Bitumen measuring device
Sensor(3pieces) | 200kgs |
12.Bitumen spraying system
After measured, bitumen is injected into mixer in form of nebulization.
Electromotor of Bitumen pump: 7.5Kw 1piece
13. Pneumatic system
Cylinder | 10pieces |
Solenoid valve | 10pieces |
Triplex part | 2pieces |
Electromotor of Air compressor | 7.5Kw(1piece) |
14. Dust collector (two grade, centrifugal and wet filter)
The first grade | double cyclone filter, reclaimed material goes into elevator directly |
Second grade | wet filter |
dust emission | ≤300mg/Nm3 |
Draught fan | 55kW(1unit) |
Water pump | 7.5kW(1unit) |
Water pump | 15kW(1unit) |
Optional:
Second grade | bag filter,impulse and reverse blowing |
Material | Nomix |
Filtration area | 324m2 |
Wind volume | 35000m3/h |
Draught fan | 55kW(1unit) |
aircompressure | 7.5kW(1unit) |
dust emission | ≤80mg/Nm3 |
15.Electric control system
Function: 1) Process of burdening with automatic control
2) Various material mixed together can be modified at any moment
3) Temperature and weight can be displayed
4)Enactment or modify run parameter conveniently
5)Error of burdening is corrected automatically
6)Numerical value of Formulation input is corrected intelligently
7)Current of each main Electromotor can be displayed
8)Manual and automatic switch
9)Process of production can be printed
10)Data memory
16.Bitumen supply system
capacity | 20m³x2 |
Bitumen injection pump | |
Capacity | 443L/min |
Electromotor | 7.5Kw |
Bitumen convey pump | |
Electromotor | 5.5Kw |
Bitumen discharge pool | |
Capacity | 3.7m³ |
17.Hot oil system
1) Heating furnace
Type | horizontal |
Capacity | 600000kcal/h |
2)
Burner | Original Italian Riello burner |
Type | automatic and temperature control oil-fired |
Capacity | 9~30kg/h |
Electromotor | 0.76Kw/h |
3)Hot oil pump
Type | gear pump |
Capacity | 50m³/h |
Circle pump | 15kW(2units) |
Oiling pump | 1.5kW(1unit) |
Hot oil System power | 20kW |
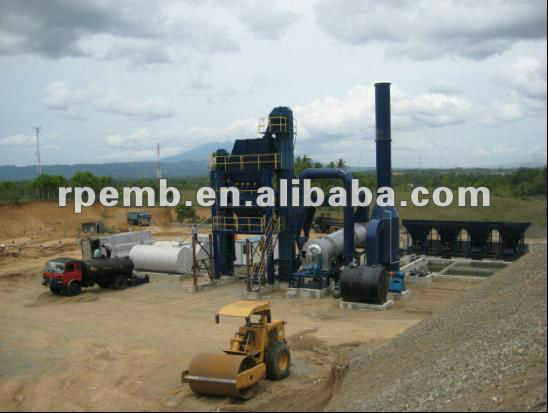
Packaging Detail:nude packing |
Delivery Detail:2 weeks after deposit |