Hematite Iron Ore Beneficiation Plant
Condition:New | Type:Magnetic Separator | Production Capacity:80% | Place of Origin:Jiangsu China (Mainland) |
Brand Name:Zhongbo | Model Number:CTB | Voltage:380V/220V/110V | Power(W):15-55KW |
Certification:BV | Warranty:1year | After-sales Service Provided:Engineers available to service machinery overseas | Application:iron ore |
Certificate:ISO9001-2000,CE,CCC | Installation:under engineer guide | Guarantee:1year | Color:As request |
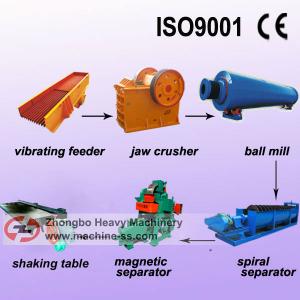
HematiteIron Ore Beneficiation Plant
I. Hematite Iron Ore Beneficiation Plant
is consisted ofJaw Crusher, Ball Mill,Classifier, Magnetic Separator, Flotation Machine, Concentrator Machine and Drier. And Equipped with Feeder, Elevator and Conveyor, a full set of hematite iron ore Beneficiation plant can be made. It has advantages such as High efficiency, Low Consumption, High Output and economical and reasonable, etc.
II.Process Flow of hematite iron ore Beneficiation plant is following:
The stone will be initiallycrushed by Jaw Crusher. Then the material with reasonable fineness will be taken to the ball mill by the elevator and feeder machine. In theball millthe material will be crushed and grinded again. Out of the ball mill the material will go to next step: Classifier. Screw Separator will wash and classify the stone mixture according their different sinking speed because of their different proportion. Then the magnetic machine will further separate the mixture material according to their magnetic ratio. After the first separation by the magnetic separator, the shaking table will separate the material again by adding special medicine in terms of the features of different stone. When the needed material has been separated, concentration machine is needed to thicken the material. At last, the material will go through the drier.
III. Technics ofhematite iron ore Beneficiation plant
Overview
Hematite is weak magnetic. And it contains mainly Fe2O3. The normal chemical composition of hematite is Fe2O3, Fe3O4, SiO2, Al2O3and so on. Based on the test report of ore provided by customer, we designed this hematite dressing technics: three stages crushing----one stage milling----two stages magnetic separation----dehydration----final product. Using this technics, we can improve the Fe content from 40% up to 64%. And the ferric oxides recovery ratio is about 70%.
Crushing and milling
Ensure the quality of raw material. And the size of ore rock should be no bigger than 400mm. The first stage and second stage we use PE jaw crusher and PEX jaw crusher. The third stage we use a double roller crusher to reduce the rock size to smaller than 10mm. We use three stages crushing to reduce the size of rock as smaller as possible. In that way, milling the ore into required fineness, 150-200 mesh, is much easier. At the end of ball mill, the milling stage, there is a screen through which the qualified ore slurry can pass through. The slurry is then sent to a magnetic separator to pick out the magnetic part of the slurry.
Magnetic Separation
After milling, the qualified slurry runs into firs stage magnetic separator, magnetic density 3500Gauss. This machine can pick out Fe3O4out of the slurry and then Fe3O4is sent to the concentrated ore pool. We use a high gradient magnetic separator in the second stage separation to pick out Fe2O3, which is weak magnetic. The picked our slurry is sent to the concentrated ore pool. Then we use a pump pull the slurry into a disc type filter to dehydrate. The output of the filter is final product and water which can recycle. The final product contains about 5% moisture. It can be stored for further usage.
Conclusion
What is narrated above is designed based on the test report of ore sample. If there is a big difference between the current sample and the ore mine, we shall modify the technics.
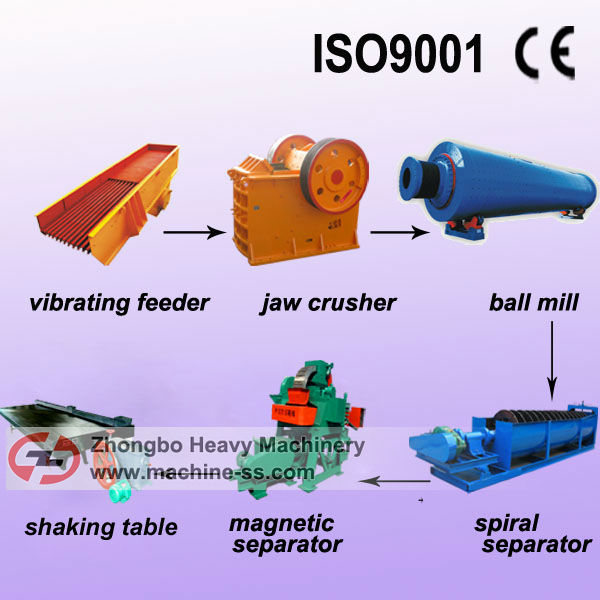
Packaging Detail:standard export packing |
Delivery Detail:in 30 days |