electrical rammer
Condition:New | Place of Origin:Shanghai China (Mainland) | Brand Name:SEHM | Model Number:ZL-B |
Voltage:380V | Power(W):150KW | Weight:10 | Dimension(L*W*H):1*1*1 |
Certification:IEC,ISO | Warranty:6 months | After-sales Service Provided:Engineers available to service machinery overseas | Application:For furnace |
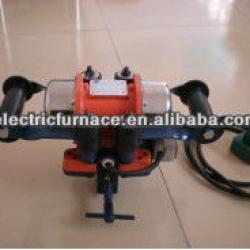
Electrical rammer
1.Accordingtothethefurnaceinner diameter,IFmelting furnacesuggested the use oftheZL-B-typeelectricfurnace building.
Model /serial numberZL-B
Rated Power(W)150
Vibrationfrequency /speed (r/min)2900
Input voltage /phase(V)400/3
Factoryvibration force(KN)
Adjustablevibration force(KN)0-2
Host weight(kg)8.8
2 ZL-B-typeelectricfurnace buildingmechanical and electricalmachine adoptsItalyITAimportedmotor, light weight, reliable quality,strongvibrationandthe advantages of uniform,IFmelting furnacesuitable for3T.
Electric furnace building machine uses low-power three-phase vibration motor, vibration frequency 2900 r / min, frequency 50Hz.Vibration force 1000-2000N, at least 0.3 ~ 0.5 MPa pressure; workers to operate motor is made of aluminum alloy shell, lighter.In order to make a more durable lining knotted.And not only be able to power up and down, but also in the furnace local rotation, bias and other sports.
3, IF melting furnace electric furnace building machine knotted requirements:
1), the minimum personnel requirements: 2 people, according to the requirement can operate, easy to learn.
2), knotted time :4-6 hours, electric Zhulu machine is not more time as long as possible, on demand operation can be.The first play furnace the knot time may be extended.
3), tie a knot: one person to operate an auxiliary, every 10 minutes to swap.Can help steady hands, without human afterburner.
4), knotted firmness: according to the capacity of the furnace, feeding and so on, can adjust the the brickwork machine vibration force, adjustable between 1000-2000N.
5), the knotting uniformity: After adjustment of the vibration force generated each time the vibration force is very uniform, pay attention when using the vibration of continuous, uniform coverage to facilitate continuous sand exhaust.
Use electric Zhulu machine making the lining, the average life expectancy increased by 10%.If experienced, can be increased by 15% -20%.
4, electric furnace building machines lining knotted advantage
1 using electric Zhulu machine, can make the layer with a layer of lining the connection between closer, but even after the sintering, can achieve the best compaction degree.
2, greatly improving the production efficiency of the lining, the average production time can be improved to 5-6 hours.
3, lower the intensity of the work of workers, the original need the work of five people, two people easily.
4, the environment is very favorable, and does not generate dust because knot.
5, knotted can greatly improve the lining life the average furnace can be increased by 10%.
6, lightweight, easy to carry and use.
5, the use of the electric furnace building machine
Construction and repair of the coil smear layer
1.For the coil coating layer at the local damage repair, clean out all debris from the coil on the smear layer, and then
Coated coil material to make the necessary repair.Note smear layer repair, to maintain smooth surface and concentric.
2.For the coil coating applied to construction, should be hung in the center of the stove a plumb line, check the installation position of the coil is concentric with the stove.The coil painting materials construction, pay attention to the the painting material embedded coil turns between the coating thickness of about 8 - 10mm, the surface should be smooth and flat.
With the introduction of institutions to demolish the old lining, coating shall be prepared for the next big small inverted cone smooth, flat inner surface.Lower coating thickness of 12 to 15 mm, or by reference to the provisions of the furnace manufacturer.The furnace nozzle 300 mm should be to minimize the slope so as to avoid in the course of analysis gap generated between the hot surface material caused by leakage of hot metal.
3.Minimize the coil bottom / top turn ring and corresponding to the bottom of an electric furnace / upper support structure (such as the pouring gate, etc.) size of the gap between the projections; its purpose is to make the support structure of the the coil coating layer with an electric furnace bottom / topform an integral smooth cylindrical surface, so that the lining expands when heated or cooled, can freely expand and contract on its smooth surface.With the above-mentioned projections or gaps between the lining to prevent the expansion and contraction of great stress, resulting in cracks lining.
4.After the completion of the smear layer with a wire brush to smear layer surface nap, in order to facilitate drying.
5.The new coil smear layer coil or a larger area of the smear layer patch layer is at least subject to natural drying period of 24 hr; the small range of the coil smear layer patch is also required by the natural drying period of at least 6 hr.
The baking of the coil smear layer specifications refer to the manual of the coil coating suppliers.Available infrared light can also be used for drying tools, the crucible mold into the furnace as the body is heated, the use of low-power heating, to take to bake evenly coil smear layer.To recommend baking temperature of 250 degrees (water-cooling of the furnace kept)
Preparatory work before rammed
1.To ensure the elimination of all the dust, refractory particles, residual waste and splashing metal remnants everything possible to fall in rammed into the lining material to the debris in the construction area, electric stove top and internal.
2.The dust cleared on the lining material bags or drums the the check material grades and specifications to meet the requirements.
3.The brickwork staff all located in the working area should be worn with pants clothing, remove the debris and pocket the easy out on the workspace.
4.Premixed lining material removed from the bag, paper bags, plastic sheets, rope and other debris should be collected, stored centrally to prevent falling to the lining material.Non-smoke rammed.
Hearth rammed
(1) the correct determination of the distance from the bottom of the furnace to the roof.Add 110% to 115% of the height in proportion to the lining material.
(2) each joined lining material, a height of 70 -90 mm.
Hearth knotting is very important, especially the bottom lining, played more solid, the more easily the lining of the long-term use.
Hearth process the first step: after feeding, with and destroyed the building fork manually hearth uniform fork two to three times.
The second step then rammed fork extension tube connected to the electric furnace building local host, hearth and even fork 3-4 times.
The third step is the bottom of the furnace vibration plate connected to the electric furnace building machine 1-2 times, hearth uniform pound.
The fourth step rammed fork then manually chopped hearth uniform fork again, head to the surface of the lining layer combination.
The fifth step and repeat the above feeding, the second feeding height can be controlled to 60-70mm.
Crucible mold is placed
1.Crucible mold into the bottom of the furnace carefully to ensure that it is placed on the horizontal.
2.The crucible mold with a plumb line is positioned at the center of the stove, in order to ensure equal wall thickness from the hearth to the roof.
3.After the positioning of the crucible mold, if the bottom of the crucible sidewall thickness unevenness equal wall thickness of the top of the crucible or the opposite case, the description the hearth lining surface is not horizontal, or crucible mold-of-roundness.At this point, should play a crucible mold re-leveling the surface of the bottom of the furnace lining or crucible mold full circle.
4.Crucible mold wedge or anchoring device fixed.Will play a frit hanging into the bottom of the crucible mold.
Sidewall rammed
1.After the crucible mold positioned and fixed, the first with rammed fork to the periphery of the crucible mold with the sidewall lining bounded by the exposed portion of the lining material fork built four times, then add the sidewall lining the material begins sidewall rammed work.Be careful not to damage the lining material or stain lining.
2.Added to the suitable charging thickness to the side wall lining materials.Lining material with a the rammed fork and shovel leveling and fork floor four times to remove air.
When blanks depths greater than 0.8 m or furnace capacity greater than 3 t should be used under the hopper feeding to prevent material segregation and dust flying.
3.Each feeding, lighting lighting carefully check whether there is any entrained debris, small metal parts and plastic or cloth fragments lining material should be removed immediately, once discovered.
4.Feeding in accordance with operating procedures and fork built until the sidewall lining material is applied to the top of the furnace.
5.The top of the electric stove rammed completed, cut the side wall of the top of the extra length (about 100 mm) backing.

Packaging Detail:Plywood package |
Delivery Detail:30 days |