Copper Rod Continuous Casting and Rolling Machine
Place of Origin:Sichuan China (Mainland) | Brand Name:141 | Model Number:UL+Z-1800+255/2+10 | usage:casting and rolling |
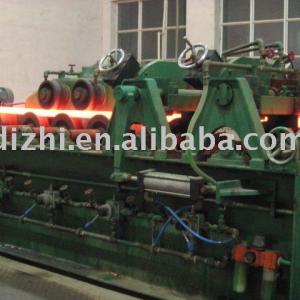
§Equipment use
1.The copper rod continuous casting and rolling machine can be equipped with different kinds of melting furnaces according to various raw materials.
2.The copper rod continuous casting and rolling machine is designed to produce φ8mm low oxygen and bright copper rods by means of continuous casting and rolling.
3.The copper rod continuous casting and rolling machine can produce ETP and FRHC with dia. 8mm.
§Equipment feature
1. Crystallizing wheel is in type of “H”, on every side of which there is an adjustable nozzle spraying water to ensure the crystal of the cast bar close and equal.
2. The copper rod continuous casting and rolling machine is with an unique rolling method combining 2-high mould with 3-high mould.
3. The copper rod continuous casting and rolling machine is with perfect outlook & lower noise and vibration.
4. The transmission system is in type of DC motor fully-digital speed adjusting.
5. The copper rod continuous casting and rolling line is easy to disassemble and assemble.
6. High efficiency & quality of production but low dissipation energy.
§Equipment composition
The copper rod continuous casting and rolling line is made up by melting furnace, 5-wheel casting machine, traction engine, rolling shear, ingot picker, oil hydraulic shear, straightener and edge shaver, cast bar brushing machine, rolling mill, Rod cooling and surface treatment unit, take-up device and electric control system.
§Technical Data
Melting furnace & Holding Furnace, copper cathode as raw material | Melting furnace type | Shaft furnace |
Capacity | 12 t | |
Holding furnace type | Hydraulic tilting -type | |
Capacity | 12 t | |
Melting furnace, when copper scraps are used | Type | Stationary reverberatory furnace |
Capacity | 60~100 t | |
Casting machine | Casting wheel dia. | Φ1800 mm |
Casting bar speed | 10.1~15.5m/min | |
Casting bar section | 2200 mm² | |
Water consumption | 170m³/h | |
Motor for casting wheel | 5.5kW (AC inverter) | |
Motor for pinch roller | 15.5kW (AC inverter) | |
Automatic shearer | Shearing length | ~700mm |
Motor | 15kW | |
Straightener & edge shaver | No. of straightening roller | 5 |
No. of shaving tools | 2 | |
Cast bar brushing machine | No. of brushing rollers | 1 |
Motor | 0.75kW | |
Rolling mill | Type | 2-highhorizontal-vertical stand in rough rolling |
3-high stand in finished rolling | ||
Outlet rod dia. | Φ8mm | |
No. of rolling stand | 12(2+10) | |
Rollers dia. | Φ255mm | |
Finished rolling speed | 7~10m/s | |
Production capacity | 12~15t/h | |
Center height | 1902.5mm | |
Main motor | 450kW (DC) | |
Emulsion consumption | 100m³/h | |
Rod cooling and surface treatment unit | Max. coolant flow-rate | 90m³/h |
Coolant pump motor | 15kW | |
Water consumption | 60m³/h | |
Rod orbital coiler | Pulling speed | 11m/s |
Pulling motor | 5.5kW (AC inverter) | |
Coiling size | Φ1400m | |
Laying head motor | 5.5kW (AC inverter) | |
Collecting basket | Φ1800×1500mm | |
Coiling weight | 3000~5000kg |
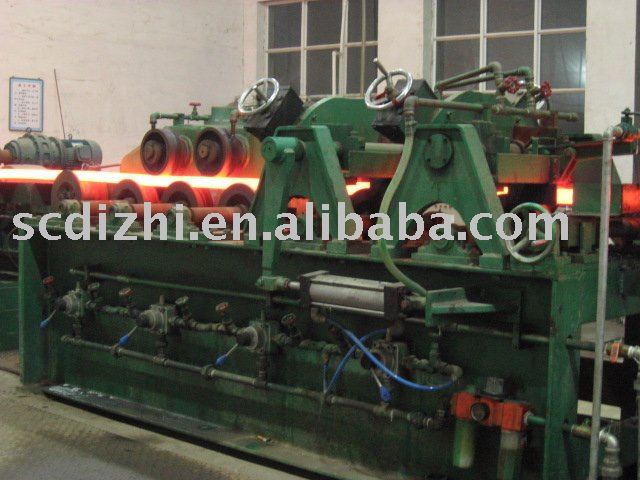
Packaging Detail:Most of the parts are naked in container, while some parts are put in container with plywood box. |
Delivery Detail:Within 70 days after receiving the 30% deposit |