China Pharmaceutical Lyophilizer
Condition:New | Type:Vacuum Drying Equipment | Place of Origin:Shanghai China (Mainland) | Brand Name:AITOMU |
Model Number:VFD | Voltage:380 | Power(W):66K | Dimension(L*W*H):5200,2200,3800 |
Weight:10 Ton | Certification:FDA | Warranty:12 M | Standard:CGMP,FDA |
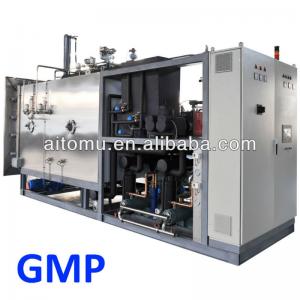
Freeze Dryer is the standard pharmaceutical Lyophilizer from Findnovo that allows users the flexibility to design their machines for their individual manufacturing requirements. Every pharmaceutical plant and system from Findnovo is a unique and efficient combination of proven technology and individual solutions reflecting the customer’s needs. Based on standard components, the company supplies plants for CGMP production configured to meet the customer's specific requirements.
Freeze Dryer is available in all production sizes from 3m² to 50m² of shelf space and more than 900kg condenser capacity to ensure high drying rates even on the largest machines. freeze dryers are equipped with safe and reliable components like reciprocating or screw compressors systems, the highly effective and proven vacuum pump system, the monitored stainless steel stoppering bellow.
Chamber
1.GB-150/PED/ASME Code Pressure Vessel.
2.cGMP guidelines and US-FDA recommendation.
3.Leak tested with helium leak detector.
4.X-ray weld tests.
5.Piping connections with sanitary clamps.
6.Sanitary clamp capped validation port on chamber.
7.All edges and corners are rounded to facilitate cleaning.
8.Dead-legs are limited to a length to diameter ratio L(length) / d(diameter) ≤3, and are sloped to ensure free draining. Where the length to diameter ratio can not beachieved, cleaning action is provided with spray-nozzle.
9.Chamber bottom is sloped to drain.
10.Cooling jackets for rapid cool down after sterilization with steam.
Door
1.Door sealing is a solid single gasket designed for high vacuum and overpressure operation.
2.Automatic locking mechanism is interlocked and controlled by PLC and its moving parts are in the machine room for easy maintenance.
3.Interlocking mechanism: the door can not be opened in case the pressure in the chamber is higher than atmospheric pressure.
Shelves
1.Shelves are cooled and heated by silicone oil circulation.
2.Specially fabricated internal channeling not only strengthens the shelves but also ensures excellent temperature uniformity.
3.Cooling and heating of shelves are PLC controlled.
4.For production freeze dryers, there are optional shelf double spacing mechanism to meet requirements of different size vials.
5.Force analysis ensures acceptable distortion after years of heating and cooling or full stoppering.
Condenser
1.Production dryers have a cooling jacket provided for quick cooling after SIP with steam.
2.Designed for high vacuum and pressurization during SIP with steam.
3.Piping connections are sanitary clamp type.
4.Includes Validation port.
5.Condenser coils are made from polished and AISI-316L stainless steel tubing.
6.The coiled piping design offers a high level of ice trapping.
7.De-icing by pure steam.
Isolation Valve
· Hydraulically or pneumatically driven
· Feedback signal during the process so as to monitor position
· Gasket in EPDM, silicone or fluorine rubber approved by FDA
Refrigeration System
1.Advanced pipeline process technology prohibits leaks.
2.World-class refrigeration units ensure reliability with long service life.
3.Each compressor has an independent circuit to cool shelves or condenser.
4.Large main valve diameter, refrigeration capacity and condenser surface area to trap a large quantity of water vapor from product in primary drying.
5.Safety protection for compressors in high head pressure, low pressure suction, motor over-temperature, differential oil pressure, unstable current, short circuit, lack phase and cooling water flow, etc.
6.Environment friendly HFC refrigerant: free of CFC and HCFC.
7.Vibration absorbers to reduce vibration and noise.
8.The flow rate of refrigerant is controlled by an expansion valve to achieve the precise temperature.
Vacuum System
1.Vacuum pump plus mechanical booster pump (for large scale freeze dryers) used to evacuate the complete system. (i.e. less than 0.01mbar vacuum)
2.Vacuum anti-suck back safety valve closes automatically in case of power outage to preserve system vacuum.
3.Optional dry pump to avoid product contamination from back-streaming vacuum oil.
Circulation System
1.Two “canned” circulation pumps provided: if one fails, the second one automatically switches on.
2.Oil free sealing pump eliminates friction during operation.
3.PID control can accurately control heating rate.
4.Driven motors keep the lowest heat transfer to thermal fluid.
5.Plate type stainless steel welded heat exchanger achieves high efficiency energy exchange.
Hydraulic System
1. At the end of the drying process, vials loaded on shelves can be stoppered either under vacuum or under a controlled atmosphere of inert gas.
2.The stoppering mechanism pressure is adjustable from 0 to 1 kg•f/cm2for proper stoppering.
3.Bellows covering the hydraulic ram prevent hydraulic oil from contaminating the chamber. Includes hardware and software integrity tests.
4.The movement of the shelves can be operated either by means of a flush mounted operator’s panel in the machine room or button on the flat sterile wall in sterile room.
Control System
1.21 CFR Part 11 and cGAMP compliance
2.Access control according to authority levels
3.Audit trail recording user actions and changes to process parameter
4.Query the curve and data table record
5.Query alarm record
6.Database management and maintenance
7.Available with manual or automatic control
8.Recipe management
CIP/SIPSystem
1.Rotary sprayer and fixed wide-angle nozzles ensure maximum cleaning coverage.
2.Pure steam sterilization minimizes contamination risks for sterile drugs.
3.Ports, gaskets and viewing glasses are suitable for high temperature.
4.The steam supply clean pipeline is made from polished stainless steel and is orbitally welded, tested and documented by endoscopic inspection.
5.Temperature control and monitoring are done at the coldest point of the system.
6.CIP/SIP runs automatically.
7.Interlocking mechanism ensures safety during sterilization process.
Vials Automatic Loading and Unloading System
· Fewer clean room personnel result in higher sterility assurance levels and reduced bio-burden.
·Automation provides operator protection when processing potent products.
·Automatic Loading and Unloading System provides higher efficiency, lower operating costs and increased equipment availability compared to manual system.
·Combining Automatic Loading and Unloading System with barrier system provides better control of risks during aseptic processing.
·Automation provides for higher repeatability and easier validation of the process.
Specification:
0.2 | 0.5 | 1 | 2 | 3 | 5 | 7.5 | 10 | 13 | 15 | 20 | 25 | 30 | 40 | 50 | ||
Usable Shelf Area | m2 | 0.27 | 0.54 | 1.08 | 2.16 | 3.24 | 5.40 | 7.56 | 9.72 | 12.96 | 14.40 | 19.73 | 24.59 | 29.60 | 41.86 | 49.34 |
Ice Capacity | kg | 4 | 10 | 20 | 40 | 60 | 100 | 150 | 200 | 250 | 300 | 400 | 500 | 600 | 800 | 1000 |
VialsCapacity (Φ22mm:~10ml) | vials | 550 | 1100 | 2300 | 4600 | 6900 | 11200 | 15700 | 20200 | 27000 | 30000 | 41300 | 51600 | 63300 | 87600 | 100800 |
Vials Capacity (Φ16mm:~5ml) | vials | 1000 | 2100 | 4300 | 8600 | 13000 | 22000 | 30800 | 39600 | 52900 | 58800 | 80900 | 101100 | 114900 | 171600 | 200000 |
Shelf Dimensions(L) | mm | 450 | 450 | 600 | 900 | 900 | 1200 | 1200 | 1200 | 1200 | 1200 | 1495 | 1495 | 1800 | 2000 | 2200 |
Shelf Dimensions(W) | mm | 300 | 300 | 450 | 600 | 600 | 900 | 900 | 900 | 1200 | 1200 | 1200 | 1495 | 1495 | 1495 | 1495 |
Number of Shelves | loaf | 2+1 | 4+1 | 4+1 | 4+1 | 6+1 | 5+1 | 7+1 | 9+1 | 9+1 | 10+1 | 11+1 | 11+1 | 11+1 | 14+1 | 15+1 |
Shelf Spacing | mm | 100 | 100 | 100 | 100 | 100 | 100 | 100 | 100 | 100 | 90 | 100 | 100 | 100 | 90 | 90 |
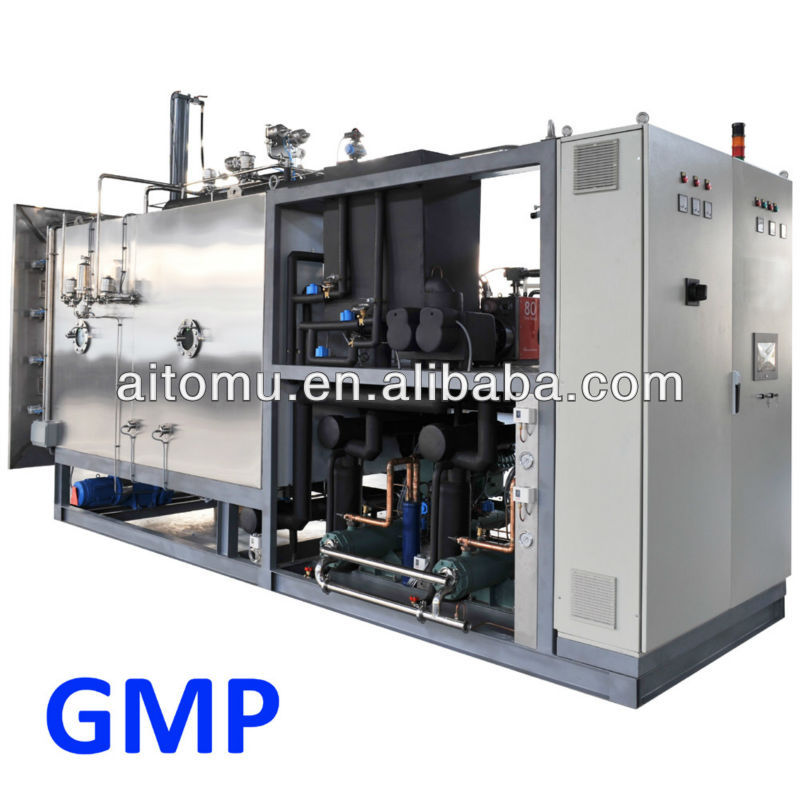
Packaging Detail:Wooden Box |
Delivery Detail:60 Days |