Aluminum Rod Continuous Casting and Rolling Machine (CCR Line)
Place of Origin:Sichuan China (Mainland) | Brand Name:141 | Model Number:LGZ-1600/Y14 | usage:casting and rolling |
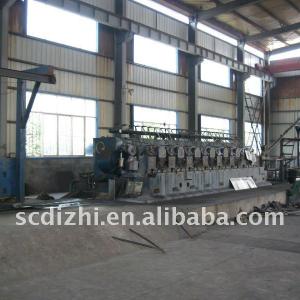
§Equipment use
Using continuous casting and rolling process, this aluminum rod continuous casting and rolling line can produce the electrical aluminum rod of dia. Φ9.5mm and the continuous rolling mill is of 14-stand.
§Equipment feature
1. The aluminum rod continuous casting and rolling line is competitive with the relative international products.
2. By adopting PLC and man-machine interface for the complete line control, it can check and display the running parameter of machines as well as indicate the breakdown.
3. The aluminum rod continuous casting and rollling machine is with perfect outlook and lower noise and vibration.
4. The machine is with an unique rolling method combining 2-high mould with 3-high mould.
5. High efficiency and quality of production & low dissipation energy.
§Equipment composition
The aluminum rod continuous casting and rolling line is composed of shaft furnace, holding furnace, 5-wheel type casting machine, front tractor, rolling shear, monorail hydraulic shear, continuous rolling mill of 14-stand, drop down coiler, electric control system, etc.
§Process flow
1. General aluminum ingot→melting furnace→holding furnace→continuous casting machine→rolling shear→ continuous rolling mill→aluminum rod
2. Molten aluminum or prepared aluminum melt flows from the holding furnace via the launder into the rotary continuous casting machine, where it is continuously casted into a pentagonal ingot with a cross-sectional area of 2300mm2. The roller shear cuts off the waste end and press it smaller or pointed so as to feed into the rolling machine, where it is rolled, and after passing through the grease box and guide pipe, aluminum rod is finally laid down in coil in the basket on the trolley.
§Technical Data
Continuous casting machine | Crystallizing wheel dia. | Φ1600mm |
Section surface of casting ingot | 2300mm2 | |
Casting speed | 16m/min | |
Crystallizing wheel rotating speed | 1.66~3.3r/min | |
Driven motor | 5.5kw | |
Type of casting machine | 5-wheel | |
Cooling water pressure | ≥0.6MPa | |
Cooling water consumption(soft water) | 100t/h (inner cooling 60t/h,outer cooling 40t/h) | |
Rolling mill in Y-type | No. of rolling stand | 14 |
Outlet rod dia | Φ9.5mm | |
Production capacity | 6T/H | |
Type | 2-high mould of 1#, 2# | |
3-high mould in “Y” type of 3#~14# | ||
Roller nominal size | Φ255mm | |
Transmission ration between capstans | 1:1.25 | |
Finished rolling speed | 8.5m/s | |
Center height | 902.5mm | |
Main motor | 350kw(DC) | |
Lubrication oil tank of gear box | 5m3 | |
Tractor | AC machine | 4KW |
Rolling shear | AC machine | 11KW |
Monorail hydraulic shear | Max. shearing force | 12000kgf |
Max. shearing stroke | 65 mm | |
Motor power | 4kw | |
Drop down coiler | Max. coiling weight | 2t (+1~10%) |
Max. coiling dia | Φ2000mm | |
Coiling driven motor power | 1.1kw | |
Trolley moving speed | 0.75m/s | |
Trolley Motor power | 2.2kw | |
Others | Overall dimension | 40×7.1×4.2m |
Total weight | 60t |
§ Detailed pictures
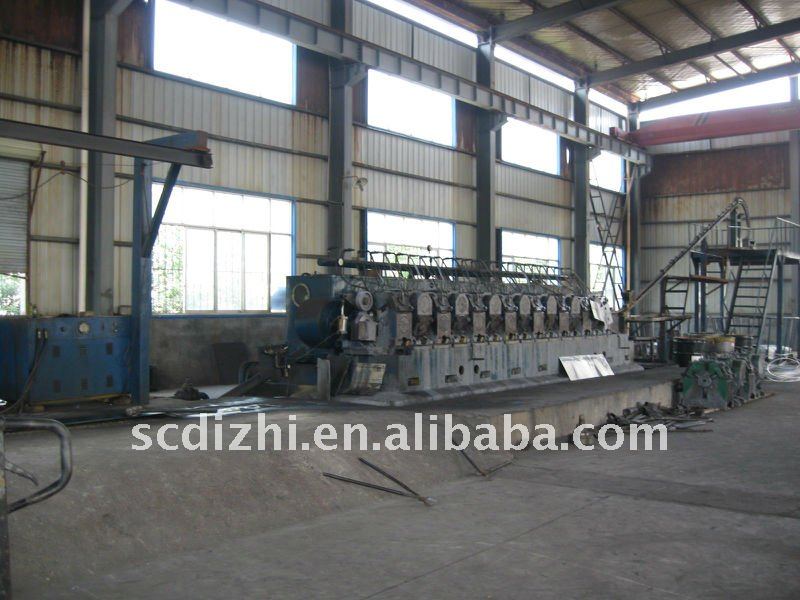
Packaging Detail:Most of the parts are naked in container, while some parts are put in container with plywood box |
Delivery Detail:Within 70 days after receiving the 30% deposit |