6-axis industrial arc welding robot
Place of Origin:Anhui China (Mainland) | Brand Name:ACCURL | Model Number:ER-16 | After-sales Service Provided:Engineers available to service machinery overseas |
Payload:16kg | Reach:1600mm | Number of axies:6 axies | Repeatability:±0.05 mm |
Protection grade:IP65 | Axis 1:±180° | Axis 2:-110°__+150° | Axis 3:-155°__+80° |
Axis 4:±360° | Axis 5:-120°__+135° |
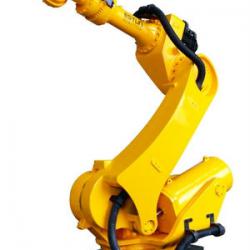
1. Machining robot
Bending efficiency has been the bottleneck of sheet metal production factory, how to reduce let bending machine of standby time, let it longer time in working state, truly obviously to improve yield.
Robot bending applicable scope:
(1) quantity and repetitive operation task.
(2) the small batch but often occur task.
(3) need two personal carried feed of ultra large parts or may give operators cause personal injury task.
2. Industrial spray painting robot
Painting has always been a harmful work since its working environments. With the new labor law emphasizing protection of the workers, robots used in painting become more and more popular.
Robot painting has the following advantages:
(1) More flexible with larger workspace;
(2) Higher quality and material utilization;
(3) Easy to operate and maintain, Offline programming largely reducing the robot tuning time;
(4) Higher utilization of machine, i.e., can achieve 90%-95%
3. welding robot
In automotive industry, the quality of welded parts is related to the safety of the vehicles. Application of robots in welding, not only enhances the quality of the parts, but also reduces the labor intensity and improves the worker’s environment. Arc-Welding robots have been widely used in automobile industry, such as, manufacturing of the chassis, chair, car rail, silencer and the hydrodynamic torque converter etc.
4. Machine loading and unloading
The traditional machine with artificial finish feeding and unloading, there is labor intensity and low efficiency, poor security problems. With the development of the production machine tool users, the automatic feeding and unloading material is CNC machine tool to realize continuous and automatic processing of the important link, the nc machine tool is an important component of the workpiece on the nc machine automation processing the premise and Bridges. To different production program of parts processing, the up-down material is qualitative different way. In the few varieties, in large quantities, single parts processing time shorter parts, using automated operation method in order to reduce the intensity of labor, increase production efficiency and reduce manufacturing cost, reduce human resources investment, robot automatic up-down material has become an inevitable trend. Robot automatic up-down material is the development trend of user mass production, this kind of machine tool using modular design, through the machine, electricity, liquid, gas control robot up-down material, can be mass product automation production. And flexible choice single, bilateral up-down material way, can mix many machine tools or other equipment, become a different production process automation production lines, with high efficiency, simple and compact structure characteristics. In the production, through the robot movement and accurate positioning, the use of hydraulic and pneumatic device control transfer material and automatic feeding and unloading material, and requirements on cutting and complete the next workpiece delivery of finished parts and already sent out, in order to shorten the production rhythm, improve production efficiency was born.
5. Packaging and Palletizing
Robot help you achieve high efficient and reliable flexible production, meet you in an increasingly shorten the product cycle, innovative packaging design, diversified packing size and product type, batch production and so on various aspects demand.
The box and tray, bag, bottles and other packaging container yards on the arrival of the dish seems very simple.
However, if faced with many harsh requirements, such as multiple conveyor line at the same time, production, packaging form frequent change in the normal operation of production line of time and very strict requirements, then only robotic automation can deal with, do a job with skill and ease. Dexterity industrial robots in building materials, home appliances, electronics, chemical fiber, automotive, food and other industries is useful.
6. Loading and unloading for hotd
China is the big manufacturing country in forging and pressing, however, the vast majority of the production process in China is completed by the manual operation, which results in low production efficiency and unstable product quality. Because of labor intensity and risk, people are reluctant to take the job. In Japan, U.S.A, Germany and other countries, robot systems and production lines in forging have been used for long time.
Robot arm can not only clamp 1100 °C -1200 °C high temperature workpiece, but also withstand vibration and shock from forging hammer. It can completely replace human’s manual forging operations such as continuous feeding, flip, unloading, such work with high risky, simple repeatability, high labor intensity. Robots in forging can effectively reduce the labor intensity and risky, improve the degree of production automation and production efficiency.
Example for automated robotic
Description of Requirements:
• The mass of workpiece for robot handling: 8kg
• The rough shape of the A-type, the first time pressing of the shape of the B-type, the finished shape of the C-shaped
• robot reach: 1500mm
• workpiece temperature: 900 °C -1200 °C
• Configuration of pressing machine: 400 tons and 630 tons electric screw pressing machine each
• Process action: Taking part from the rack → Putting into the first machine → Taking forging part from the second machine →Putting into the feed box→Taking part from the first machine→Transferring to the second machine→Taking part from the rack
Program configuration:
• An ER16 (16kg 1600mm) robot;
• A robot grasper with pneumatic actuation (cylinder and fixture material can withstand high temperature with 1200 °C, meeting the requirement of grasping operation in different stages );
• A robot base ( based on the pressing machine’s geometry parameters);
• A conveyor for raw materials;
•A conveyor for finished products;
• Security fence;
• Auxiliary electrical control system
• Cooling unit (installed by the robot end-user according to the specification)
• Other auxiliary equipment
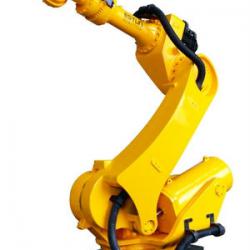
Packaging Detail:wooden case |
Delivery Detail:20 day |